The vessels of our multi-chamber casting furnaces feature an integrated inductor that separates the inflow chamber from the homogenizing chamber. Both chambers are connected via several induction channels in which the molten metal is thoroughly mixed during heating. In addition to the mixing effect, the induction heating process also facilitates exact bath temperature control.
Our compact, modular furnaces are successfully used in numerous copper production facilities as high-precision dosing and deoxidation units. Other typical applications include holding and superheating molten steel and NF-metals such as aluminium, and metal bath microalloying and homogenizing. These furnaces are also used to separate slag from the alloy and retain the slag before casting. The alloy is discharged from the furnace via a forehearth fitted with a stopper control system. By controlling the metal inflow from an upstream holding furnace and measuring the weight of the alloying furnace, the bath level inside the alloying furnace can be kept almost constant, ensuring a repeatable casting result.
Benefits at a glance:
- Precise dosing of alloying agents
- Good mixing characteristics
- Fully homogenized metal baths
- High repeatability
- Minimum energy use
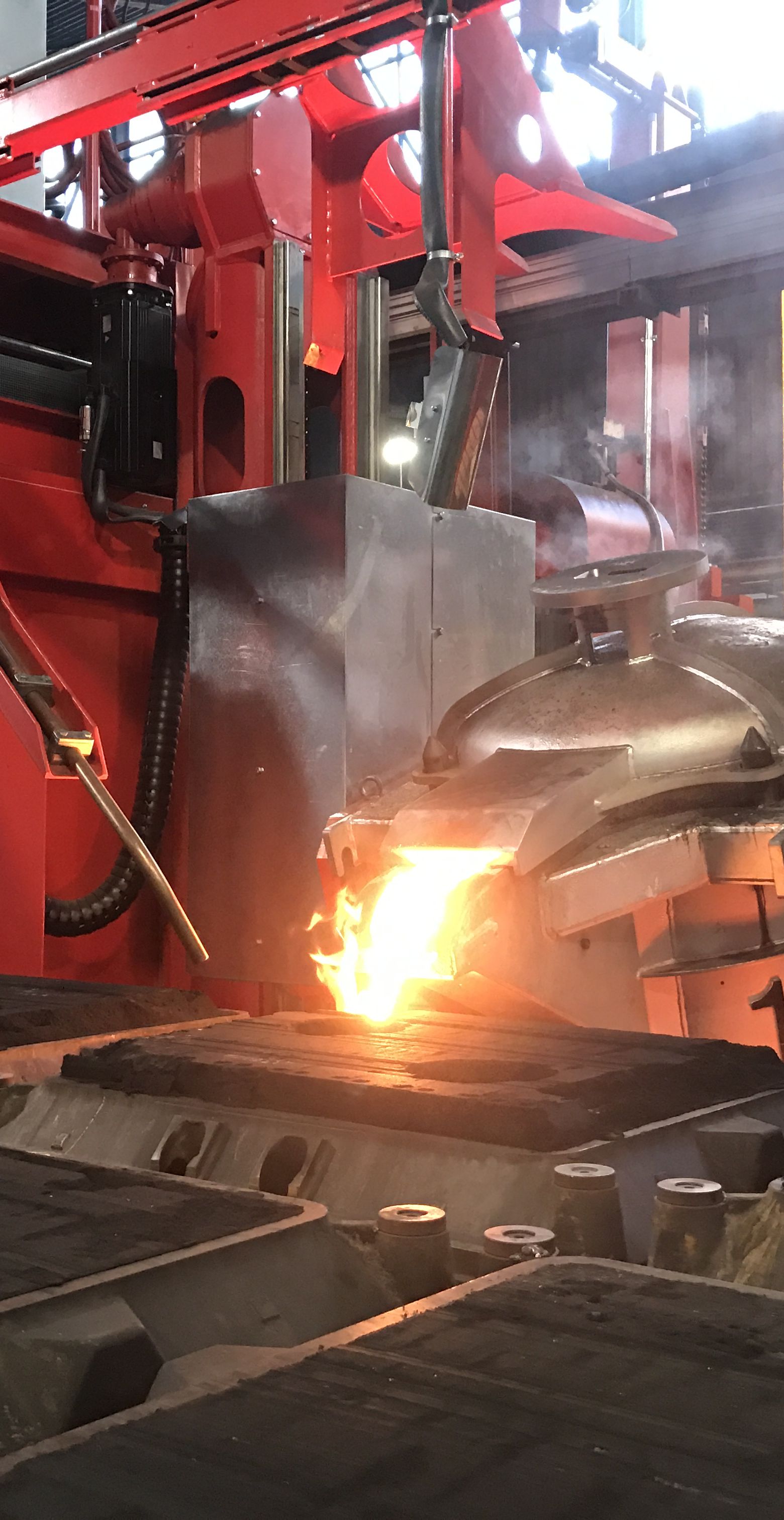
A typical application: Oxygen-free copper
Exact metering of phosphorus additions, thorough mixing and complete homogenization of the metal bath are decisive in producing phosphorus-deoxidized copper alloys (DHP copper). Therefore, the oxygen and residual phosphorus contents in the metal bath are continuously measured. Based on these measurements, deoxidizing agents can be added in precisely the quantities needed to achieve the chemical composition specified. This method has replaced the previously common method of adding phosphorus-copper in the transfer launder between the holding furnace and the continuous casting plant – a practice that no longer complies with current analytical accuracy requirements.
Typical uses | Dosing, micro-alloying, homogenizing, holding, superheating, deslagging, vertical continuous casting |
Metals | Copper, aluminium and tin alloys |
Design | Hydraulically tiltable |
Capacity | From 2 up to 20 t |
Electrical power | From 100 up to 600 kW |
Downloads
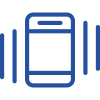
Phone +49 2473 601-710
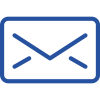
E-Mail info@induga.de