In large-series casting of aluminium-silicon alloys for the automotive industry, the molten metal delivered by third-party suppliers is stored in furnaces designed to hold the metal exactly at the specified temperature.
These storage furnaces ensure homogeneous temperature distribution within the metal bath and efficient, economical holding of molten metal. The closed design of the furnace vessel prevents any undesired gas absorption. As the furnace is inductively heated, there is no loss due to combustion.
The metal is discharged via a pressurized ascension pipe. This guarantees that no contaminated metal is entrained into any of the downstream process steps. Scum removal from the aluminium bath and cleaning of the channel inductor require only very little effort.
Benefits at a glance:
- Exact temperature control
- Homogeneous temperature distribution
- Pure alloys
- Negligible metal loss due to combustion
- Easy cleaning
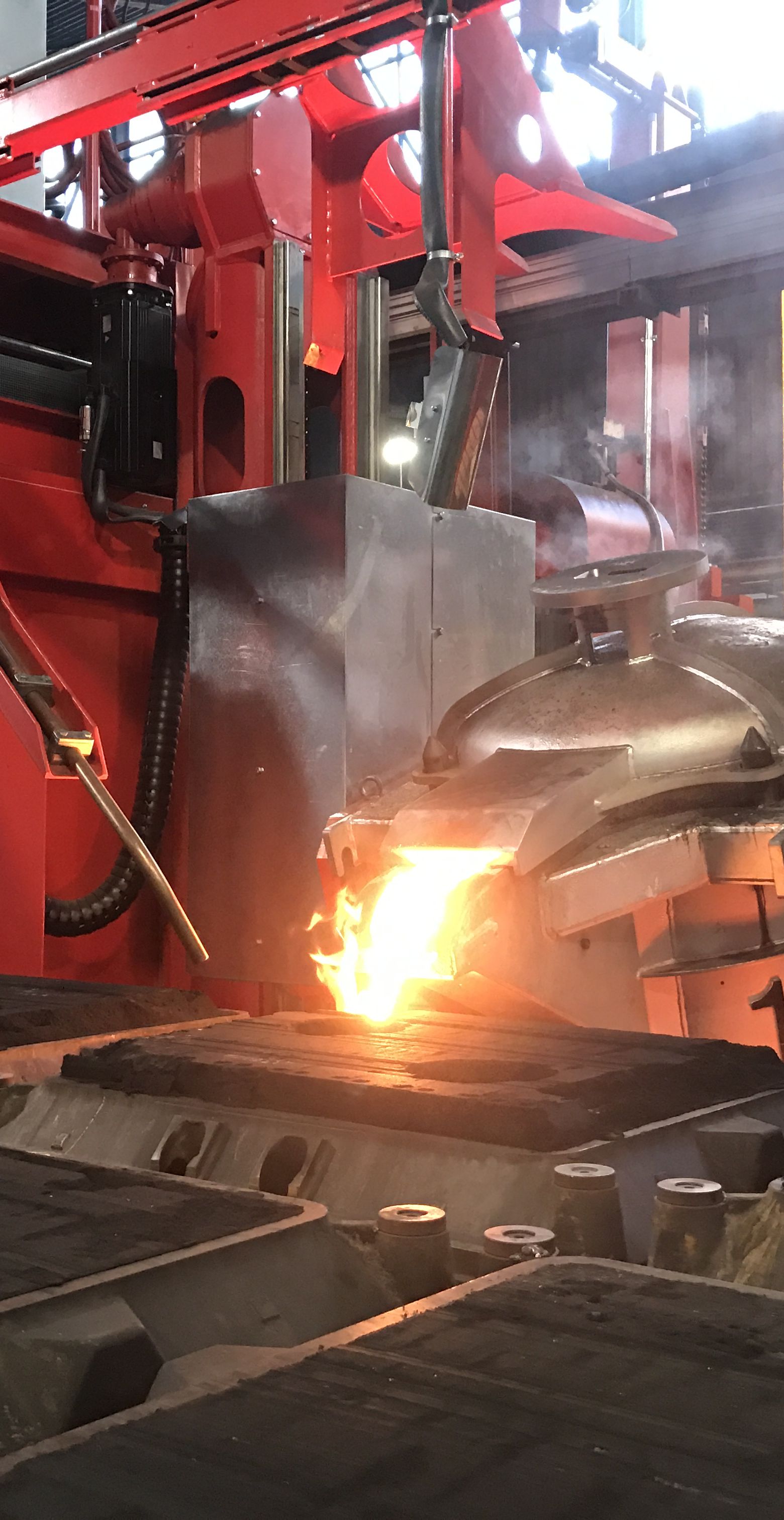
Our storage furnaces for aluminium alloys consist of a ceramic-lined, closed cylindrical furnace vessel with a flanged-on channel-type inductor. The molten metal, produced in inhouse meltshops or sourced from external suppliers, is filled into the furnaces via an inlet fitted at the side.
The furnaces are emptied via a siphon pressurized with air or inert gas. They are fitted with a maintenance lid to facilitate cleaning and slag removal.
Design | Channel-type induction furnace |
Furnace type | Stationary |
Tapping mode | Batch-type |
Capacity | From 3 up to 25 t |
Electrical power | From 60 up to 200 kW |
Typical use | Storage of aluminium and aluminium alloys |
Downloads
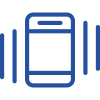
Phone +49 2473 601-710
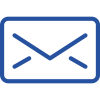
E-Mail info@induga.de