Drum-type induction furnaces are mainly used in continuous and batch-type melting and casting lines for the melting, holding, storing and homogenizing of copper, aluminium and zinc alloys. A typical use is the production of high-purity, oxygen-free copper alloys.
The furnace vessel is eccentrically arranged between two rotating discs. The filling port and the spout are positioned in the furnace’s axis of rotation. To discharge the molten metal – continuously or discontinuously –, the furnace is rotated so that metal from the lower part of the bath can flow out via a siphon.
Benefits at a glance:
- Closed design
- Clean furnace atmosphere
- High bath homogeneity
- Low radiation losses
- Easy replacement of inductors
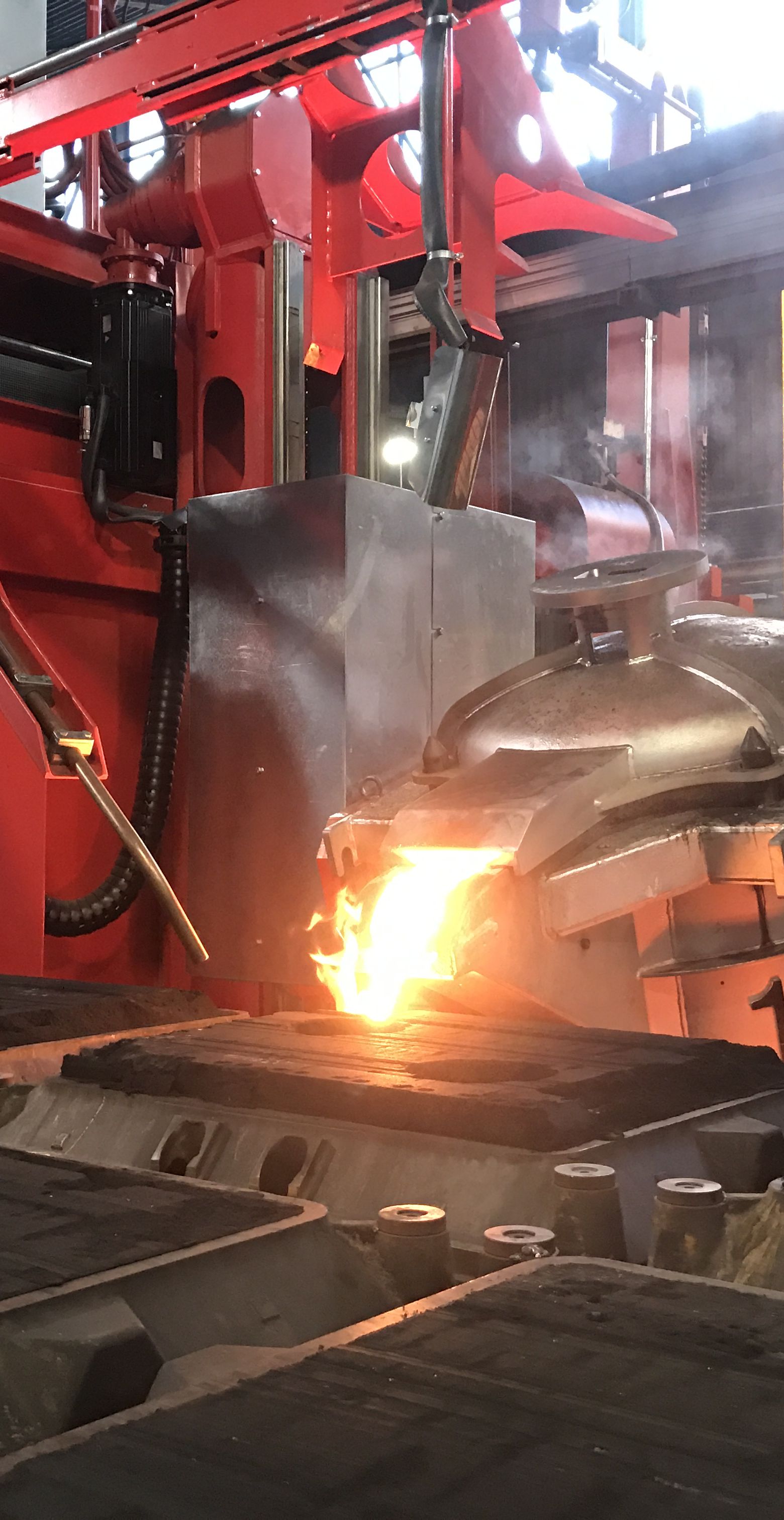
Cathodes, scrap, recycling material or ingots can be fed in using charging machines, cranes or conveyor belts. Molten metal is fed in via transfer launders or casting tundishes.
Metals | Non-ferrous metals (copper, Al and Zn alloys) |
Input material | Cathodes, scrap, recycling material, ingots, molten metal |
Temperature | Up to 1,250 °C |
Design | Drum-type furnace, rotatable, inductively heated, 2 or 4 channel-type inductors |
Capacity | From 12 up to 70 t (with copper) |
Throughput | Up to 12 t/h with two inductors, or 24 t/h with four inductors |
Electrical power | Up to 4 x 2,000 kW |
Downloads
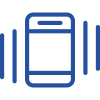
Phone +49 2473 601-710
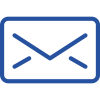
E-Mail info@induga.de