A pressurized pouring furnace with semi- or fully automatic stopper control for automatic sand moulding lines, carrousel-type casting plants and casting machines.
The INDUMAT® consists of a main furnace chamber with two flanged-on siphons. One siphon serves as the inlet, the other – fitted with a forehearth – as the outlet. The main chamber can be fitted with a channel- or crucible-type inductor, depending on the metal processed. The closed design of the INDUMAT® and the option to render the furnace atmosphere inert ensure that the absorption of gas by the molten metal is reduced to an absolute minimum.
The precise pressure control in the main furnace chamber and the bath level measurement in the forehearth guarantee that the metallostatic pressure acting on the metal in the casting nozzle corresponds at all times to the casting weight specified for each individual flask.
Benefits at a glance:
- Precise pouring rate control
- Precise control of bath level in the funnel
- Minimal gas absorption
- Uninterrupted pouring
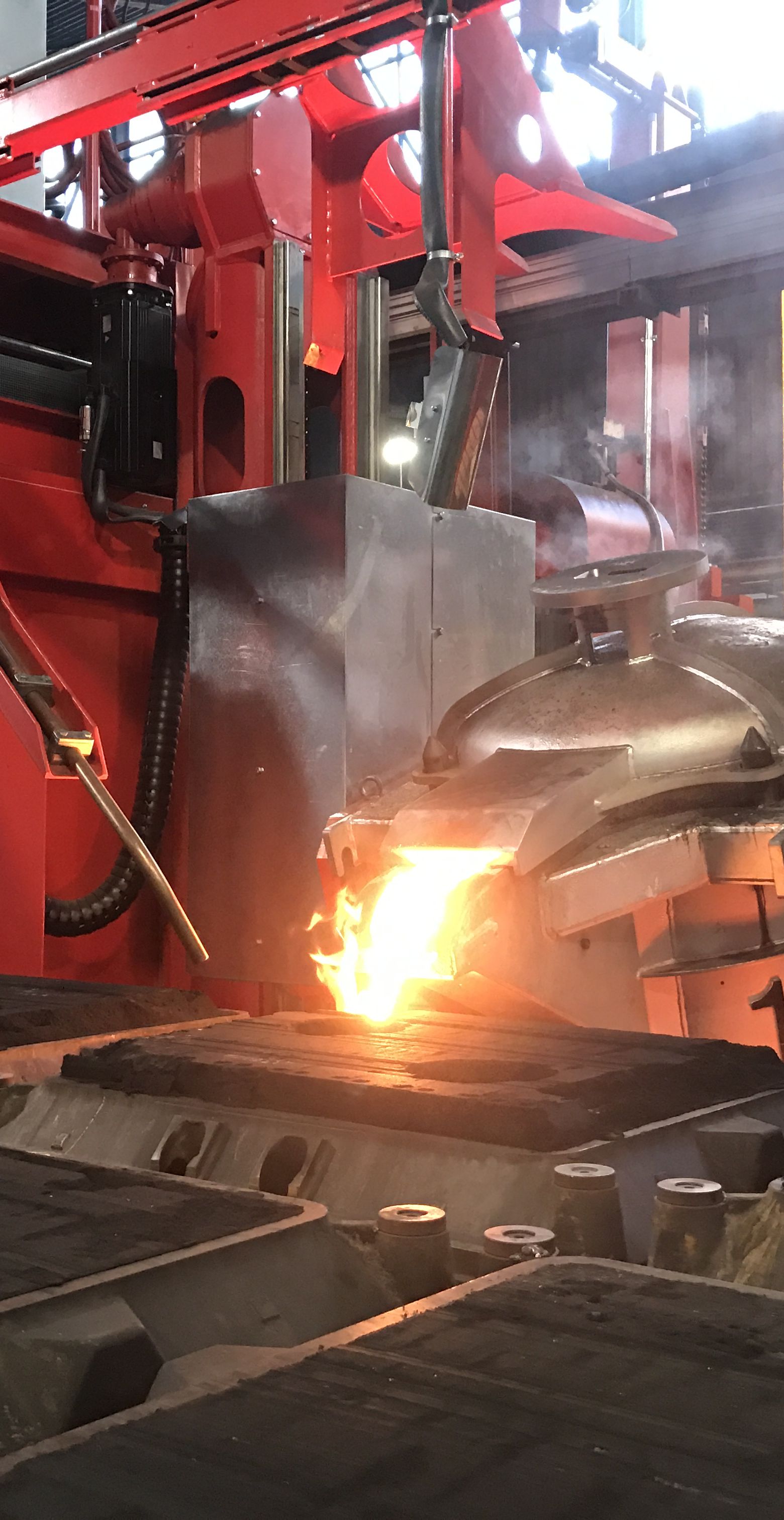
The rate at which the metal is discharged from the furnace is controlled by a stopper system fitted above the nozzle. After a teach-in, the stopper plug movement can be precisely controlled by the flask filling degree. Alternatively, the stopper can be accurately controlled by measuring the furnace weight with load cells or by optical bath level control in the funnel. This ensures repeatability of the specified pouring curve.
The Indumat enables uninterrupted pouring: Using controlled pressure reduction in the main chamber, both metal pouring and refilling can be performed at the same time.
Our foundry customers use Indumat pouring furnaces that are stationary in design and those able to move through two axes to precisely adjust them to the respective pouring funnel position.
Capacity | From 2 up to 40 t |
Heating capacity | From 60 up to 1,200 kW |
Temperature | From 700 up to 1,700 °C |
Throughput | From 1 up to 20 t/h |
Downloads
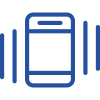
Phone +49 2473 601-710
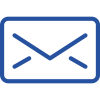
E-Mail info@induga.de